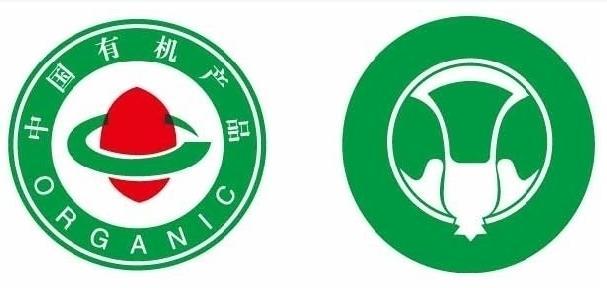
我们都知道,关键点的设立,是根据“判断树”推出而需实施监控的要点,通俗说是下阶段下工序不可控或纠正成本不经济而设立关键控制点,比如:饮料罐装工序,罐装压盖后发现容量过多或过小,都不可能重新开盖再补灌,那么,通常在罐装压盖时设立CCP点:罐装速度、压盖高度、旋转压力等参数,早在开机时就进行核实和验证,设定首件产品验证及一定时间间隔进行核实。
在某一供港澳鲜活禽产品加工厂,该企业在原料进厂验收和产品开膛等2工序设立了CCP点,却忽视了生产过程产品裸露时间和温度的控制要求,导致了生产过程时间过长、温度过高而导致微生物大量繁殖,虽然后工序实施急冻,但微生物只是处于休眠状态,一到解冻后检测往往超标准要求。
二、产品不分类,没有对每一个产品进行逐一进行危害分析、制定切实的HACCP计划。
在某一输美水产品生产企业,从《鱼肉制品、鱼肉制品的HACCP计划》中发现:该公司没有逐一对产品进行描述,没有对每一个产品逐一进行危害分析,“鱼肉制品”没有描述是哪一种鱼、哪一种肉、什么包装形式、制品是怎样的状态(如冷冻/保鲜/罐头)及贮运条件等等,不同的鱼和不同的肉因其原料品种的不同,存在不同的危害,不同的包装形式和不同的制品状态决定了其加工设备/方法及其危害是不同的,CCP就会不一样,本例“鱼肉制品的HACCP计划”,把所有鱼肉制品混为一谈,没有逐一进行危害分识别特定危害实施控制。这种完全违反HACCP基本原理的“鱼肉制品HACCP计划”。显然是不可能控制食品安全危害的。
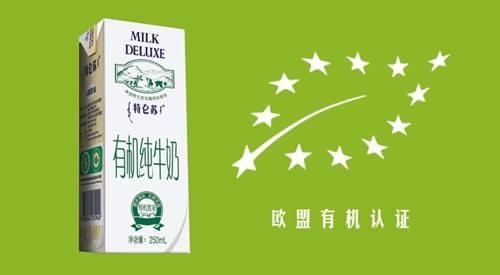
因此,作为HACCP验证员,我们要求该企业要按照CAC《HACCP体系及其应用准则》的规定,重新对其每一种鱼、每一种肉为原料加工的每一种包装形式的产品,根据其生产工艺设备和加工方法逐一进行危害分析,重新识别各工序工艺要求,制定适合的HACCP计划.